Weaving our way through Zari workshops
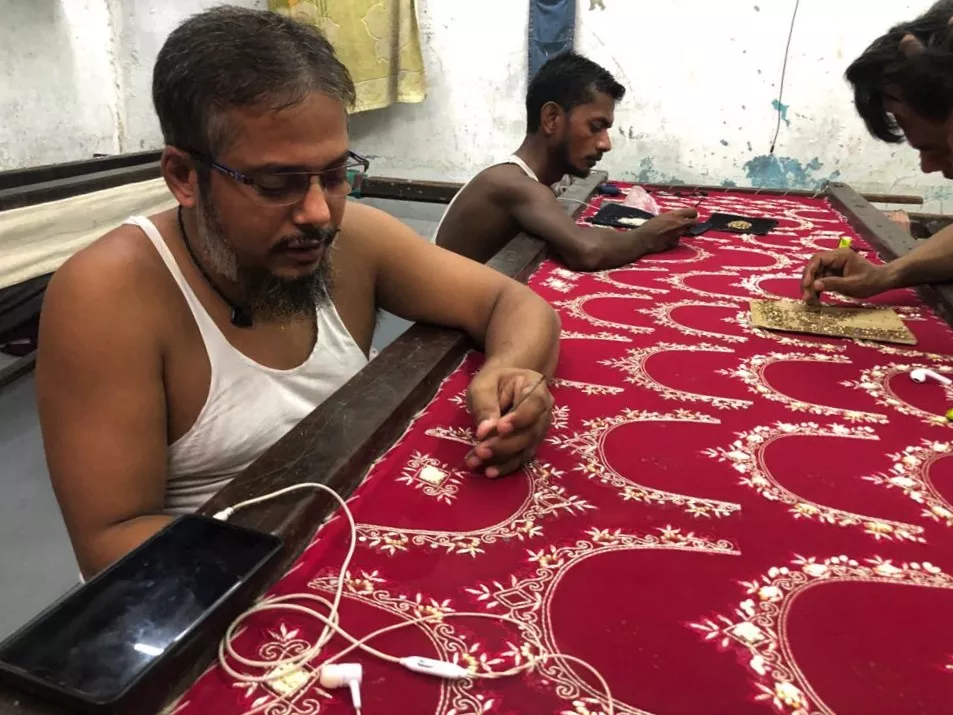
Weaving our way through Zari workshops
Zari work takes place in smaller pockets of Dharavi and the work done is intricate and detailed which requires long work hours. This is a very local process where multiple elements from different parts of Dharavi come together to form a final product. It starts with drawing out designs which are then sent for imprinting of the design and finally it goes for stitching. The product made from these steps is still in the form of a raw material which is given to a garment dealer or a tailor who would make a finished garment out of it.
The making of the design
Moghen Ansari is a trained designer who draws out intricate zari designs. His workplace is a
1.5 X 2 meter rented shop. Moghen Bhai receives reference photos from his clients which he starts drawing freehand on a gateway paper. He makes small changes according to his expertise to make each design unique. The cost ranges from Rs. 50-500 according to the time taken and the intricacy of the work. On a daily basis, he works on four to five such orders. The designs are then sent to artisans who work on the embroidery.
The making of the zari work
After receiving the design from Moghen Bhai, Mohammad takes up the job. Mohammad has a workshop on the second floor which is a 4.5 X 3.8 meter space. Three to four artisans work simultaneously on one piece of cloth. In the workshop, there is an adjustable wooden frame on which the cloth is stretched and the artisans sit around it to carry out zari work. The process starts with getting the cloth from the nearest cloth shop. This cloth is then stretched onto a wooden frame which is adjusted according to the size of the cloth. The design received from Moghen Bhai is then imprinted on the cloth with the help of carbon paper. Each design is handwoven with different threads and jari coils. The stitching techniques used are unique to each design and create different patterns. After the weaving is finished, jewels, pearls, and sparkles are stuck using a flat sticking tool. The complete process of zardosi takes at least two to three days. The stitched jari patch is then sent to a tailor or a garment retailer for them to convert it into a finished garment or product.
The zari industry in Dharavi is highly spread out since the zari work does not require large spaces or complex tools to be carried out. We see workshops in small houses in the inner gali’s of Dharavi. Besides a workshop, another network of this industry can be seen amongst the women, who take small orders of making zari patches and carry out this work within the comfort of their homes.